1. Introduction
Organic fertilizer pelletizers are crucial equipment in the production of organic fertilizers. Their stable and efficient operation is essential for ensuring the continuous production of high – quality organic fertilizer granules. Regular and proper maintenance is the key to extending the service life of organic fertilizer pelletizers, reducing equipment failures, and maintaining high production efficiency. This article will comprehensively introduce the daily maintenance key points and skills of organic fertilizer pelletizers.
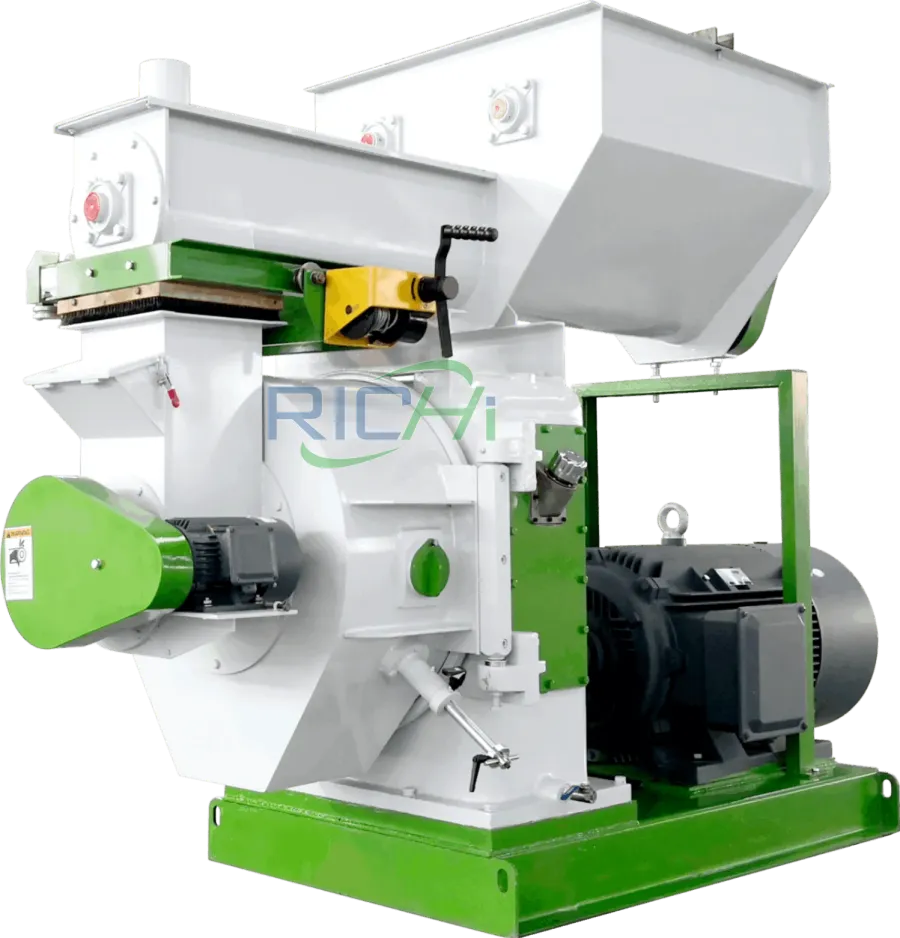
2. Importance of Daily Maintenance
2.1 Prolonging Equipment Lifespan
The components of Organic Fertilizer Pellet Machines, such as rollers, dies, screws, and motors, are constantly under stress during operation. Abrasion, corrosion, and fatigue can gradually damage these components. Through daily maintenance, such as regular cleaning, lubrication, and inspection, the wear rate of components can be effectively reduced, thereby prolonging the overall lifespan of the equipment. For example, if the rollers and dies of a compression pelletizer are well – maintained, their service life can be extended by several months to years, saving significant costs for equipment replacement.
2.2 Ensuring Stable Production
Malfunctions of organic fertilizer pelletizers can disrupt the production process, leading to production delays and increased costs. Regular maintenance can detect potential problems in advance, such as loose parts, abnormal wear of components, and electrical system faults. By addressing these issues promptly, stable production can be ensured. For instance, if a small crack in the die of a pelletizer is detected during daily inspection and repaired in time, it can prevent the die from breaking during production, which could otherwise cause a long – term shutdown of the production line.
2.3 Improving Product Quality
The quality of organic fertilizer granules is closely related to the performance of the pelletizer. A well – maintained pelletizer can ensure that the granulation process is stable, resulting in granules with uniform size, shape, and density. On the contrary, if the equipment is not properly maintained, problems such as uneven granulation, abnormal particle shapes, and inconsistent densities may occur, reducing the quality of the final product. For example, if the rotation speed of the rollers in a compression pelletizer is unstable due to bearing wear, the formed pellets may have different sizes.
3. Daily Maintenance Key Points
3.1 Cleaning
Equipment Surface Cleaning
Regularly clean the surface of the organic fertilizer pelletizer to remove dust, dirt, and adhered organic materials. Dust and dirt can accumulate on the equipment surface, not only affecting its appearance but also potentially causing corrosion over time. Adhered organic materials can harden and interfere with the normal operation of moving parts. Use a clean cloth or a soft – bristle brush to wipe the surface. For stubborn stains, a mild detergent solution can be used, but make sure to dry the equipment thoroughly after cleaning to prevent rust. (Related post:Organic Fertilizer Production Line)
Interior Component Cleaning
The interior components of the pelletizer, such as the inside of the feed hopper, the channels in the extrusion part, and the space around the rollers and dies, also need to be cleaned regularly. Organic raw materials may adhere to these areas, which can affect the flow of materials and the granulation process. In some cases, it may be necessary to disassemble certain parts for thorough cleaning. For example, the die of a compression pelletizer can be removed and cleaned to ensure that the die holes are unobstructed.
3.2 Lubrication
Bearing Lubrication
Bearings are critical components in organic fertilizer pelletizers, as they support the rotation of rollers, screws, and other moving parts. Regular lubrication of bearings is essential to reduce friction and wear. Select the appropriate lubricant according to the operating conditions of the equipment, such as high – temperature – resistant lubricants for components operating at high temperatures. The lubrication frequency depends on the usage frequency of the equipment. For frequently used pelletizers, bearings may need to be lubricated once a week, while for less – used ones, once a month may be sufficient. Use a grease gun to inject the lubricant into the bearing lubrication points.
Gear and Chain Lubrication
If the pelletizer is equipped with gears or chains for power transmission, these components also require regular lubrication. Gears and chains are prone to wear due to high – torque transmission. Lubrication can reduce wear and noise, and improve the transmission efficiency. Special gear oils or chain lubricants should be used. When lubricating gears, make sure to apply the lubricant evenly on the tooth surfaces. For chains, spray the lubricant along the length of the chain.
3.3 Inspection
Component Inspection
Regularly inspect the key components of the organic fertilizer pelletizer, including rollers, dies, screws, belts, and motors. Check for signs of wear, cracks, deformation, or looseness. For example, the surface of the rollers should be smooth, and any signs of pitting or grooves may indicate excessive wear. Dies should be inspected for wear of the die holes, which can affect the size and quality of the pellets. Screws in extrusion pelletizers should be checked for wear and damage to the threads. Belts should be inspected for looseness or cracks, as loose belts can cause slipping and affect the transmission of power. Motors should be checked for abnormal noise, vibration, and temperature rise.
Electrical System Inspection
The electrical system of the pelletizer is also an important part of the inspection. Check the wiring for any signs of damage, such as exposed wires or loose connections. Test the electrical switches, relays, and control panels to ensure their proper functioning. Measure the voltage and current of the electrical components to detect any abnormal values. For example, an abnormal increase in current may indicate a problem with the motor or a short – circuit in the electrical system. (Related project:10-12T/H Organic Fertilizer Production Plant In Ecuador)
4. Maintenance Skills
4.1 Component Replacement Skills
When a component is found to be severely worn or damaged during inspection, it needs to be replaced in a timely manner. For example, when replacing the die of a compression pelletizer, first, turn off the power and ensure the safety of the operation. Then, carefully remove the old die using appropriate tools, such as wrenches. Clean the mounting surface of the die before installing the new die. Make sure to align the new die correctly and tighten the fixing bolts to the specified torque. After installation, test the operation of the pelletizer to ensure that the new die functions properly.
4.2 Troubleshooting Skills
During the operation of the organic fertilizer pelletizer, various problems may occur. Operators and maintenance personnel should have basic troubleshooting skills. For example, if the pelletizer produces pellets with inconsistent sizes, possible causes may include uneven feed of raw materials, wear of the die holes, or unstable rotation speed of the rollers. First, check the feed system to ensure that the raw materials are fed evenly. Then, inspect the die for wear. If necessary, adjust the rotation speed of the rollers through the control system. If the equipment emits abnormal noise, it may be due to bearing damage, gear misalignment, or the presence of foreign objects in the moving parts. In this case, stop the equipment immediately, disassemble the relevant parts for inspection, and take appropriate measures to solve the problem.
4.3 Calibration Skills
Some components of the organic fertilizer pelletizer, such as pressure sensors, speed sensors, and weighing devices in the feed system, need to be calibrated regularly to ensure accurate measurement and control. For example, to calibrate a pressure sensor in a compression pelletizer, use a standard pressure source to apply known pressures to the sensor. Compare the output signals of the sensor with the actual pressure values and adjust the calibration parameters of the sensor according to the deviation. Calibration should be carried out according to the manufacturer’s instructions and relevant standards to ensure the accuracy and reliability of the equipment.
5. Case Studies of Effective Maintenance
5.1 Case 1: A Small – Scale Organic Fertilizer Producer
A small – scale organic fertilizer producer regularly maintained its compression pelletizer. By following a strict cleaning schedule, lubricating the bearings and gears every two weeks, and inspecting the components weekly, the producer was able to extend the lifespan of the rollers and dies from the original six months to over a year. The production process became more stable, with fewer equipment failures. As a result, the production efficiency increased by about 15%, and the quality of the produced organic fertilizer granules improved, leading to an increase in customer satisfaction.
5.2 Case 2: A Medium – Sized Organic Fertilizer Plant
A medium – sized organic fertilizer plant trained its maintenance personnel on advanced maintenance skills, including component replacement and troubleshooting. When a problem occurred with the extrusion pelletizer, such as uneven extrusion of granules, the maintenance team was able to quickly identify the problem as a worn – out screw. They replaced the screw within a few hours, minimizing the production downtime. Through continuous improvement of maintenance skills and regular maintenance, the plant reduced its equipment – related production losses by about 30% and improved the overall productivity of the production line.
6. Conclusion
In conclusion, the daily maintenance of organic fertilizer pelletizers is of great significance for the smooth operation of the organic fertilizer production process. By mastering the key points and skills of maintenance, such as cleaning, lubrication, inspection, component replacement, troubleshooting, and calibration, the lifespan of the equipment can be extended, stable production can be ensured, and product quality can be improved. Case studies have shown that effective maintenance can bring significant economic and production – related benefits. In the future, with the continuous development of organic fertilizer production technology, the maintenance requirements for organic fertilizer pelletizers may also change, and relevant personnel need to keep learning and updating their knowledge to better maintain these important pieces of equipment.