Belt dryers are essential equipment used in various industries for drying materials such as food, chemicals, and biomass. Ensuring that a belt dryer operates efficiently and effectively is crucial for maintaining product quality and optimizing production processes. One of the best ways to verify the performance of a belt dryer is through functional testing. This article outlines the key steps and considerations involved in conducting functional tests on a belt dryer.
1. Understanding Functional Testing
Functional testing involves evaluating the performance of a belt dryer against its specified operational criteria. This process helps identify any issues that may affect the efficiency and effectiveness of the drying process. Key aspects to be tested include airflow, temperature control, drying time, and moisture content of the final product.
2. Preparing for Functional Testing
Before conducting functional tests, it is essential to prepare adequately:
- Review Manufacturer Specifications: Familiarize yourself with the manufacturer’s specifications and operational guidelines for the belt dryer. This information will serve as a benchmark for evaluating performance.
- Gather Necessary Equipment: Ensure that you have the necessary tools and equipment for testing, including thermometers, hygrometers, anemometers, and moisture meters. These instruments will help measure temperature, humidity, airflow, and moisture content accurately.
- Establish Testing Procedures: Develop a clear testing protocol that outlines the steps to be followed during the functional testing process. This protocol should include safety precautions, measurement methods, and data recording procedures.
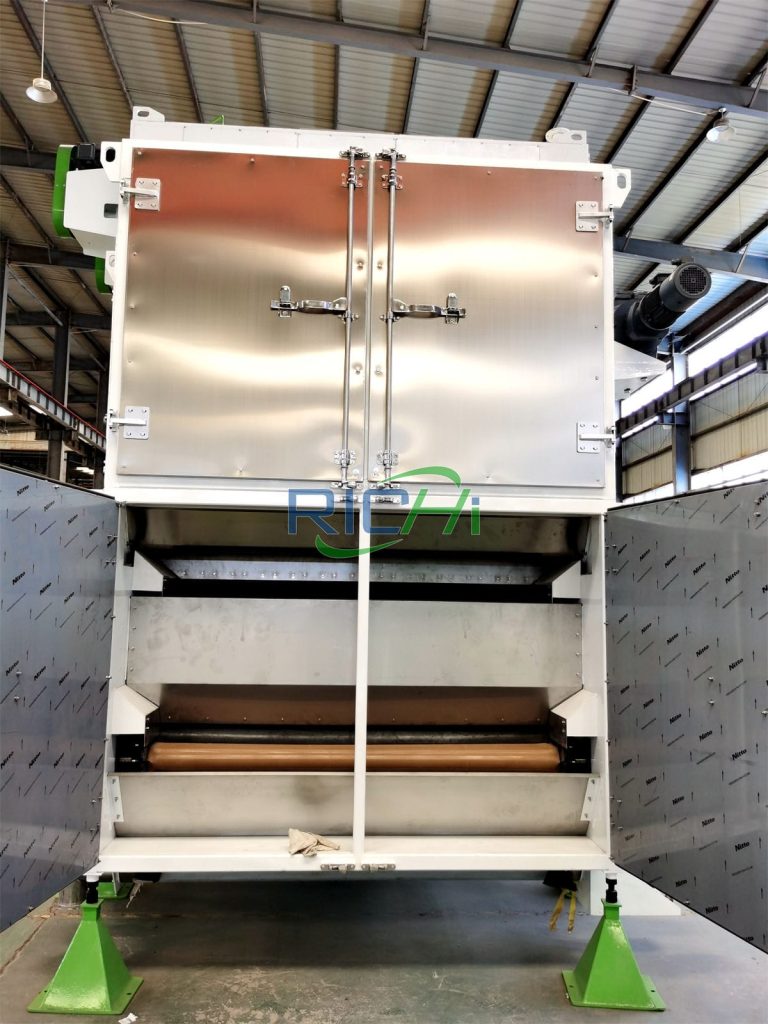
3. Conducting Airflow Tests
Airflow is a critical factor in the drying process, as it influences the efficiency and effectiveness of moisture removal.
- Measure Airflow Rate: Use an anemometer to measure the airflow rate at various points in the drying chamber. Ensure that the airflow is consistent and meets the specifications outlined by the manufacturer.
- Check Air Distribution: Assess the uniformity of airflow across the drying bed. Proper air distribution is essential for achieving even drying. Look for any dead spots where airflow may be insufficient, which can lead to uneven drying and product quality issues.
- Evaluate Fan Performance: Inspect the performance of the fans responsible for circulating air within the dryer. Ensure that they are operating at the correct speed and are free from obstructions that could impede airflow. (Related post: pet food dryer)
4. Testing Temperature Control
Temperature control is vital for ensuring that materials are dried effectively without overheating or damaging the product.
- Monitor Temperature Settings: Use thermometers to measure the temperature at various points in the drying chamber. Compare these readings to the set temperature parameters to ensure that the dryer is operating within the desired range.
- Check Temperature Uniformity: Assess the uniformity of temperature throughout the drying chamber. Inconsistent temperatures can lead to variations in drying performance and product quality.
- Evaluate Heating Elements: Inspect the heating elements for proper operation. Ensure that they are functioning efficiently and providing consistent heat. Any irregularities in heating can affect the overall drying process.
5. Measuring Drying Time
Drying time is a critical factor that impacts production efficiency and product quality.
- Determine Initial and Final Moisture Content: Before starting the drying process, measure the initial moisture content of the material using a moisture meter. After the drying cycle, measure the final moisture content to determine the effectiveness of the drying process.
- Record Drying Times: Track the time taken to achieve the desired moisture content. Compare this with the expected drying time specified by the manufacturer. Significant deviations may indicate issues with the dryer’s performance.
- Assess Product Quality: Evaluate the quality of the dried product. Look for signs of over-drying or under-drying, such as changes in texture, color, or flavor. High-quality dried products should meet the required specifications for moisture content and appearance.
6. Conducting Moisture Content Tests
Moisture content is a key indicator of the effectiveness of the drying process.
- Use Moisture Meters: Employ moisture meters to assess the moisture content of the dried product. This measurement should be taken at multiple points to ensure accuracy and consistency.
- Compare with Specifications: Compare the measured moisture content with the target moisture content specified by the manufacturer. If the moisture content is outside the acceptable range, it may indicate issues with the dryer’s performance.
- Evaluate Consistency: Assess the consistency of moisture content across different batches of dried product. Variations in moisture content can affect product quality and marketability.
7. Documenting Test Results
Accurate documentation of test results is essential for evaluating the performance of the belt dryer:
- Record Findings: Maintain detailed records of all measurements, observations, and test results. This documentation will serve as a reference for future evaluations and troubleshooting.
- Analyze Data: Analyze the collected data to identify trends or patterns that may indicate performance issues. Look for correlations between airflow, temperature, drying time, and moisture content.
- Report Issues: If any performance issues are identified during testing, report them to the maintenance team or management promptly. Timely action can prevent further complications and ensure the continued efficiency of the dryer.
8. Continuous Improvement
Functional testing should be an ongoing process to ensure the long-term performance of the belt dryer:
- Regular Testing Schedule: Establish a regular testing schedule to monitor the performance of the dryer over time. This proactive approach can help identify potential issues before they impact production.
- Implement Improvements: Use the findings from functional tests to implement improvements in the drying process. This may include adjusting operating parameters, upgrading components, or modifying maintenance practices.
- Training and Awareness: Ensure that operators are trained in the importance of functional testing and the proper procedures for conducting tests. A well-informed team is better equipped to identify and address performance issues.
Conclusion
Verifying the performance of a belt dryer through functional testing is essential for maintaining optimal efficiency and product quality. By conducting thorough tests on airflow, temperature control, drying time, and moisture content, operators can identify potential issues and ensure that the dryer operates effectively.Investing time and resources in functional testing not only enhances the reliability of the belt dryer but also contributes to overall operational efficiency and cost savings. As industries continue to seek efficient drying solutions, prioritizing functional testing will be crucial for maintaining a competitive edge in the market. By focusing on these practices, manufacturers can achieve significant improvements in productivity and profitability.