Belt dryers are essential industrial equipment used for drying a wide range of materials, including food products, chemicals, and biomass. One of the critical aspects of a belt dryer’s operation is its air system, which plays a vital role in ensuring efficient and uniform drying. This article explores the various air system components of a belt dryer machine, their functions, and their impact on the drying process.
1. Overview of Belt Dryers
A belt dryer operates by passing a continuous conveyor belt through a series of drying zones where hot air is circulated around the material being dried. The air system is responsible for providing the necessary airflow, temperature control, and humidity management to achieve optimal drying results. The efficiency of the air system directly affects the overall performance of the belt dryer, influencing energy consumption, drying time, and product quality.
2. Key Air System Components
The air system of a belt dryer typically consists of several key components:
a. Airflow Fans
Airflow fans are crucial for circulating hot air throughout the drying chamber. They ensure that the air reaches all areas of the material being dried, promoting even drying.
- Types of Fans: Belt dryers may use axial or centrifugal fans, depending on the design requirements. Axial fans are generally used for high airflow rates, while centrifugal fans provide higher pressure and are suitable for systems requiring more resistance.
- Performance Monitoring: Regularly checking the performance of airflow fans is essential. Monitoring airflow rates and pressure can help identify any issues, such as blockages or fan malfunctions, that could affect drying efficiency.
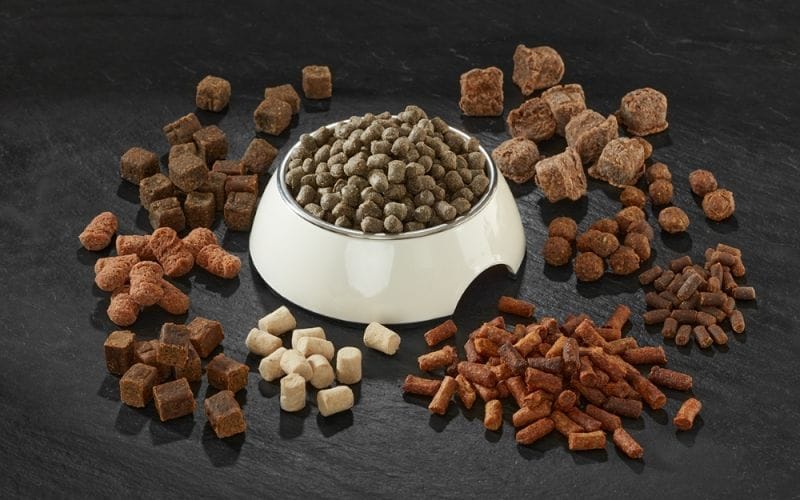
b. Heating System
The heating system is responsible for providing the necessary heat to the air that will be circulated through the dryer.
- Heating Methods: Common heating methods include electric heaters, gas burners, and steam heating. The choice of heating method depends on the specific application and energy availability.
- Temperature Control: Accurate temperature control is vital for effective drying. The heating system should be equipped with thermostats and control valves to maintain consistent temperatures throughout the drying process.
c. Air Distribution System
The air distribution system ensures that the hot air is evenly distributed across the material on the belt.
- Ductwork and Diffusers: Properly designed ductwork and diffusers facilitate uniform airflow and minimize dead spots where moisture may not be effectively removed. Adjustable dampers can be used to control airflow to different sections of the dryer.
- Impact on Drying Efficiency: An efficient air distribution system helps achieve uniform drying, reducing the risk of over-drying or under-drying specific areas of the material. This uniformity is crucial for maintaining product quality.
d. Exhaust System
The exhaust system is responsible for removing moisture-laden air from the drying chamber.
- Ventilation: Proper ventilation is essential for maintaining optimal humidity levels within the dryer. The exhaust system should be designed to efficiently remove moist air while preventing the entry of outside air that could affect the drying process.
- Condensation Management: In some applications, it may be necessary to manage condensation that forms in the exhaust system. Proper design and insulation can help mitigate issues related to condensation, preventing damage to the equipment and ensuring consistent operation. (Related post:pet food dryer )
3. Importance of Air System Quality
The quality of the air system components significantly impacts the overall performance of the belt dryer:
- Energy Efficiency: High-quality fans, heating elements, and air distribution systems can reduce energy consumption by maximizing airflow and minimizing heat loss. This efficiency translates to lower operational costs and improved profitability.
- Product Quality: Uniform drying is essential for maintaining the quality of the final product. Inconsistent air distribution or inadequate temperature control can lead to variations in moisture content, affecting product integrity and marketability.
- Operational Reliability: Reliable air system components reduce the likelihood of breakdowns and maintenance issues. Regular inspections and maintenance of fans, heating systems, and exhaust systems contribute to the longevity and reliability of the belt dryer.
4. Regular Maintenance and Checks
To ensure the air system components of a belt dryer operate effectively, regular maintenance and checks are essential:
- Routine Inspections: Conduct routine inspections of fans, heating elements, and ductwork to identify any signs of wear or damage. Look for loose connections, corrosion, or blockages that could affect airflow.
- Performance Testing: Regularly test airflow rates and temperature control to ensure the air system is functioning as intended. Use anemometers to measure airflow and thermometers to monitor temperature levels throughout the drying process.
- Cleaning: Keep air ducts and fans clean to prevent dust and debris from obstructing airflow. Regular cleaning helps maintain optimal performance and prevents potential fire hazards.
5. Conclusion
The air system components of a belt dryer machine play a crucial role in ensuring efficient and effective drying processes. Understanding the functions of airflow fans, heating systems, air distribution systems, and exhaust systems is essential for optimizing performance and maintaining product quality.By prioritizing the quality of these components and implementing regular maintenance checks, operators can enhance the efficiency and reliability of their belt dryers. As industries continue to seek efficient drying solutions, investing in high-quality air system components will be essential for maintaining a competitive edge in the market. By focusing on these aspects, manufacturers can achieve significant cost savings, improve operational efficiency, and ensure the production of high-quality dried products.